Nike Have Changed Their Supply Chain and Logistics Strategy
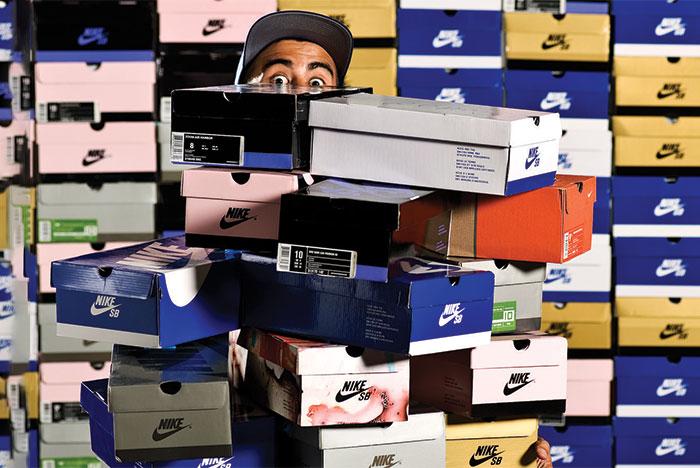
have just come out with a detailed explanation of how they’ve changed their logistics strategy to ensure customers are still receiving shoes while keeping their global workforce safe. As per , they’ve boiled down their extensive overhaul to four key points.
Firstly, Nike have added more distribution centres to their North American operations, which, prior to the winter of 2020, had only been based in Memphis. That has since expanded into additional regional centres in Los Angeles, Bethlehem and Dallas to serve all four corners of the continent. Over in Europe, shoes will be coming in and out of Madrid in addition to a Belgium outpost.
AI and machine learning technology has also helped prioritise orders and deliveries, with additional pickup and postage options for customers for online and physical retail. While over 1000 robots in Nike’s distribution centres has begun taking on more physically strenuous tasks like picking and packing.
The revamped distribution also means an opportunity for Nike to rethink their packaging and delivery methods. Of course, this means sustainability is at the forefront. This being considered by using more recycled content in their shoeboxes and offering ground shipping, which creates lower carbon emissions.
Finally, at a human level, the has remained the top priority during the pandemic. Continued sick leave and pay support for the company’s essential workers has been implemented, plus academic mentorship in partnership with the University of Memphis to aid career development.
For a deeper analysis of how the sneaker industry at large has been affected by supply chain issues, click .